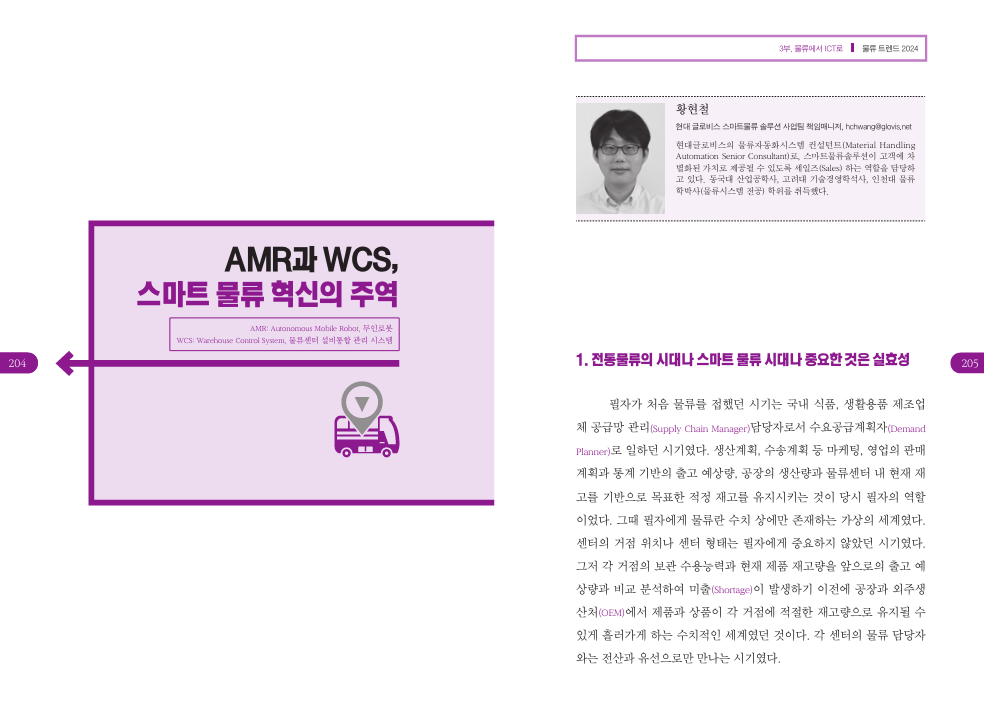
AMR과 WCS, 스마트 물류 혁신의 주역
- 이용 기한
- 3일 (오늘 구매시 2025.08.24까지 이용가능)
황현철 현대 글로비스 스마트물류 솔루션 사업팀 책임매니저, hchwang@glovis.net
현대글로비스의 물류자동화시스템 컨설턴트(Material Handling Automation Senior Consultant)로, 스마트물류솔루션이 고객에 차별화된 가치로 제공될 수 있도록 세일즈(Sales) 하는 역할을 담당하고 있다. 동국대 산업공학사, 고려대 기술경영학석사, 인천대 물류학박사(물류시스템 전공) 학위를 취득했다.
필자가 처음 물류를 접했던 시기는 국내 식품, 생활용품 제조업체 공급망 관리(Supply Chain Manager) 담당자로서 수요공급계획자(Demand Planner) 로 일하던 시기였다. 생산계획, 수송계획 등 마케팅, 영업의 판매 계획과 통계 기반의 출고 예상량, 공장의 생산량과 물류센터 내 현재 재고를 기반으로 목표한 적정 재고를 유지시키는 것이 당시 필자의 역할이었다. 그때 필자에게 물류란 수치 상에만 존재하는 가상의 세계였다. 센터의 거점 위치나 센터 형태는 필자에게 중요하지 않았던 시기였다. 그저 각 거점의 보관 수용능력과 현재 제품 재고량을 앞으로의 출고 예상량과 비교 분석하여 미출(Shortage)이 발생하기 이전에 공장과 외주생산처(OEM)에서 제품과 상품이 각 거점에 적절한 재고량으로 유지될 수 있게 흘러가게 하는 수치적인 세계였던 것이다. 각 센터의 물류 담당자와는 전산과 유선으로만 만나는 시기였다.
당시 필자에게 물류센터는 가상의 공간이기에 필자가 APS(Advanced Planning System) 에 입력한 수송, 생산계획 지시 등을 어떻게든 현장에서 해결해 주겠지 하는 바람이 있었던 것 같다. 지나친 입고량으로 인해 물류센터 담당자가 물류센터 내부에 화물을 더 이상 둘 곳이 없다고 물류 현장에서 볼멘소리를 하거나, 통합허브센터(Central Distribution Center)에 서 매일 새벽까지 지역거점센터(Regional Distribution Center)로 수송되어 당일 배송까지 이루어지는 작업인 크로스 도킹(Cross-Docking) 업무를 수치만 보고 지나치게 많은 작업량을 한꺼번에 지시하여 현장 작업이 지연되는 경우도 필자의 현장에 대한 이해 부족으로 발생하곤 했었다. 물류 운영이라는 것이 물동량뿐만 아니라 운영 프로세스, 물류센터의 작업환경 등 모든 것이 어우러지지 않으면 효율이 나지 않는다는 것을 그 당시 필자는 이해하지 못하고 있었던 것이다.
이후 3PL을 전문으로 하는 물류 전문기업의 물류 전문연구원으로서 물류 컨설턴트가 되었을 때 ‘어찌되었든 물류에서 알아서 해결해 주겠지’ 하던 누군가의 역할이 필자의 역할이 되었다. 식품, 특히 소비재(CPG) 제조업에 근간한 필자의 산업 경험과 식품제조사, 식자재 유통, 뷰티 소비재를 유통하는 그룹 계열사의 물류용역 이외에도 주로 소비재 영역의 물류운송 및 보관을 담당하던 이전 물류전문기업의 물류 사업영역이 유사하여 필자는 한동안 생활물류라 할 수 있는 소비재, 식품, 유통의 물류 위주로 컨설팅 업무를 수행하였다. 초기에는 SCM의 전공을 살려 미래 물동량 예측 및 생산성 분석 업무를 담당하다가 차츰 물류센터 설계, 물류 운영 개선(Process Innovation, PI)업무로 영역을 확장하게 되었다.
이 시기를 통해 물류 센터의 역할이라는 것이 단순히 물리적 수용능력(Capacity)만을 고려하는 것이 끝이 아니라 인력관리, 작업 프로세스, 수익구조 등 모든 것이 어우러져 판단되어야 하는 것임을 배울 수 있었다. 특히 어떤 개선 과제건 간에 단순 아이디어 도출로 마무리되지 않기 위해서는 결국 손익이 타당한가와 개선 아이디어의 실현이 가능한가, 실행 시 위험(risk)은 최소화된 아이디어인지가 중요했다.
과거 10년 전 3PL 물류 컨설팅은 물류센터 내에서 프로세스 상의 의미 있는 개선 효과를 거둘 만큼 다양한 설비가 존재하지 않았던 시기였기에 입고, 보관, 피킹, 출고로 이루어지는 물동량 데이터 분석과 현장 내부의 정성적 분석에 공을 많이 들였다. 고객의 요구사항, 사업 환경, 분석된 물동량 데이터, 현장 인터뷰 등의 시사점을 바탕으로 물류 프로세스를 변경하는 해결방안을 제시하여 고객에게 가치를 제공하는 것이 핵심 전략 중 하나였다. 보관영역은 대부분 팔렛트랙과 선반랙에 의존하였고, 박스나 소물( 小物, 작은 물건) 피킹에 관해서는 반자동설비인 DPS(Digital Picking System), DAS(Digital Assorting System) 를 주로 사용하고 있었다. 가장 첨단으로 여겼던 자동화 솔루션 또한 자동 분류기(Soter System) 정도였다.
전통물류 시기와 현재 시기의 물류센터 운영의 가장 큰 차이는 입고, 보관, 피킹, 포장, 이송 등 모든 프로세스에 다양한 장비와 설비가 도입되어 활용되어지고 있다는 점이다. 기술적 이해를 바탕으로 설비를 조합하면, 물류 프로세스 전 영역을 작업자 중심이 아닌 자동화 시스템 중심으로 운영 변경이 가능하다는 점이 큰 차이이자 변화라고 생각한다. 하지만 그렇다고 물류센터의 본질이 바뀐 것은 없다. 전통 물류의 시기에서도 현재의 시기에서도 물류센터의 역할과 가치는 화물이 훼손 없이 이동, 보관되는 것이고, 이러한 행위들은 필수적으로 경제성이 담보되어야 한다.

물류자동화 컨설팅 업무를 담당하며, 여러 산업군의 고객들을 만났을 때 인터넷 매체를 통해 다양한 설비를 접할 기회가 늘어나다 보니 새로운 종류의 참신한 설비 검토를 원하지만, 실제 투자를 검토하는 의사결정 과정에서 최종 선택되는 자동화 시스템을 보면 동종업계의 레퍼런스가 있어 운영상에 경제성이 검증된 설비를 선택하는 고객이 대부분이었다. 물류자동화 센터에 대해서는 첨단의 다양한 시도도 중요하겠지만, 결국은 한정된 예산 아래 실패 위험을 최소화하여 투자하고, 문제없이 안정적으로 물류자동화 센터가 운영되는 것이 가장 중요하기 때문이라 판단된다. 설계 기간은 정해져 있는데 투자하지 못할 기술 검토에 시간을 너무 소비하거나 반대로 과거 본인이 경험한 설비만 선호하였을 경우 기대한 만큼의 운영 효과를 내지 못할 가능성이 높다. 그렇다면 어떻게 물류자동화 센터를 설계하는 것이 실효성 높고, 안정적으로 센터운영을 가능하게 할까? (중략)
AMR: Autonomous Mobile Robot, 무인로봇
WCS: Warehouse Control System, 물류센터 설비통합 관리 시스템
※ 내용이 더 궁금하시면 구매를 부탁 드립니다.